COMPANY
INSIGHT
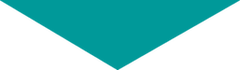
SELECTING THE RIGHT TECHNOLOGY FOR MANUFACTURING DIGITALIZATION IN MEDICAL DEVICE AND DIAGNOSTICS
With the questions of whether and when to begin implementing Smart Manufacturing already substantially answered – yes and now – MedTech firms must navigate the question of how their digital transformation will take place. Decisions in this realm are of considerable consequence.
Technologies designed to support manufacturing digitalization are flooding the market, each with different impacts on the shape of a company’s digital enterprise. Under these conditions, it is far better to have a transformation plan determine the technologies you choose, rather than having those technology choices dictate the characteristics and performance of the digital enterprise.
The question for you as a competitive MedTech company is: Which is the better starting point? And the short answer is: Whichever one best meets your growth and innovation objectives. In general, a modern and integrated Manufacturing Operations Management (MOM) system is emerging as the best choice for Smart Manufacturing in growth-oriented companies.
Let’s explore some of the key technological requirements to perform an effective implementation of MOM digital solutions in Medical Device and Diagnostics.
Portfolio modularity – Top MOM solutions are modular and extend from advanced scheduling to cross-functional quality management and production execution capabilities to manufacturing intelligence solutions. Portfolio modularity better serves your company by accommodating focused initial investments, rapid success and ROI, followed by additional reinvestment to grow your digital manufacturing footprint.
Flexible and industry-specific functionalities —Based on years of industry experience and several implementations, best-in-class MOM providers have developed out-of-the-box (OOTB) or pre-configured capabilities specific to MedTech operations and processes. At the same time, they know that also need to adapt their digital manufacturing solution to plant-specific needs that cannot be replicated. Thus, effective MOM solutions must provide the right balance between OOTB capabilities for standard MedTech processes and flexible functionalities for custom requirements through zero-code configuration tools.
Common interoperability system – Comprehensive and effective MOM solutions require each module to focus on specific production domains, while a common interoperability system grants a seamless data flow between them and makes sure that the right information is rapidly delivered where needed, at the right time.
Cross-functional integration and closed-loop – ISA-95, the International Society of Automation’s standards for the automated interface between enterprise and control systems, organizes the digital manufacturing enterprise into a four-layer stack. Critical to an effective enterprise is a seamless integration between Level 3 (MOM), Level 4 (Business planning and logistics, such as PLM and ERP) and shop-floor automation through the same common interoperability system. This integration enables the implementation of Digital Twins in real production and activates continuous closed-loop improvement through as-planned and as-is data comparison.
Smart data and IoT actionable information – Traditional manufacturing execution systems have been implemented to transform paper-based processes into digital manufacturing and compliance operations only. This is now evolving. MedTech firms recognize that stand-alone systems are data rich but information poor, and they need integrated solutions to drive key insights from the manufacturing shop floor to management departments. Modern MOM solutions must leverage on vertical integration with the shop floor to transform production big data into IoT actionable analytics (smart data), and transfer them to enterprise intelligence capabilities to take smart and strategic decisions for efficiency and quality improvements.
Modern usability and mobility — A modern and user-friendly software interface is critical to ensure operators, supervisors and inspectors to efficiently navigate the system. Access to this interface should be enabled for any kind of device, including: smartphones, tablets, laptops and high-resolution monitors.
Anticipating cloud opportunities – Cloud-ready MOM platforms are crucial to increase the speed of deployment during implementation stages and reduce the total cost of ownership.
On a broader scale, an integrated MOM solution with best-in-class functionalities and modern technologies generates significant business benefits because it incorporates greater sophistication of capabilities, smarter usability and better connectivity with other systems. Important to the MD&D industry, integrated MOM also leads to efficiency in regulatory compliance. Using an integrated MOM, MedTech companies are able to enforce product quality excellence and process consistency across the manufacturing value chain.
Their manufacturing and quality departments can anticipate, react, contain, correct and prevent defects more easily through cross-functional quality processes provided by enterprise collaboration. Quality issues can be identified at any level (design, engineering, scheduling, production, and more) and integrated operations will approach product quality proactively.
Other benefits include global flexibility, enterprise collaboration, faster ROI and lower risk with a stepwise approach to implementation, and happier stakeholders because the digital systems are built to their particular needs.