COMPANY
INSIGHT
Add Russia to your additive map
Secrets of the Russian Additive Market Revealed by TEN MedPrint, the fast-growing
contract manufacturer
The following are a few of the key medical applications where ElectroCraft motors empower medical motion control.
Individual implants came into mass use with the advent of the additive technology. Increasingly advanced production technologies are allowing for a greater number of operations to be carried out using individual implants that significantly improve the postoperative quality of life. This includes the restoration of bones following injuries and tumor removal surgeries, as well as joint and intervertebral cartilage replacement. By 2019 the global market of additive implants has exceeded 400,000 operations per year.
In 2017, the number of operations involving individual 3D-printed implants in Russia was merely dozens. Luckily, a few daring venture investors took up the challenge of bringing new technologies into the country. One of them poured funds into a contract company TEN.MedPrint engaged in 3D-printing for medical use.
Two years later, TEN.MedPrint is now collaborating with the largest centers for post-trauma and reconstruction surgery in the country and taking part in various work groups that are paving the way for updates in legislation. The company steadily delivers thousands of items each year. The number of operations featuring additive implants in Russia has reached a thousand, and keeps rising rapidly.
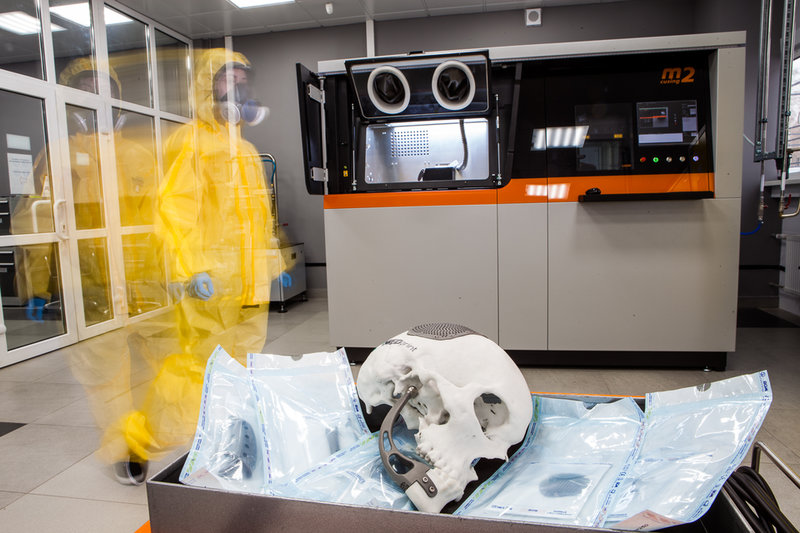
Each 3D-printed implant comes with a conformity certificate
How many companies are currently present in the Russian market?
There are fewer than five producers of additive medical items in Russia. However, TEN.MedPrint is the only independent contract company that accepts orders from any clients and has the full set of documents for all production stages, from engineering to the final product.
What are the market prospects?
We look into the future with optimism. Medical additive items manufactured by TEN.MedPrint in Russia comply with ISO 13485. However, the price of an individual or serial implant made in Russia is up to three times lower than of its European counterparts. Each item comes with a conformity certificate.
Russian legislation on the clinical use of individual additive implants in Russia is still only being developed, and TEN.MedPrint is actively involved in the work group to pave the way for it.
There is a rule in place that gives priority to products made in Russia when it comes to public procurement, which means that entering the Russian market will suggest localized production.
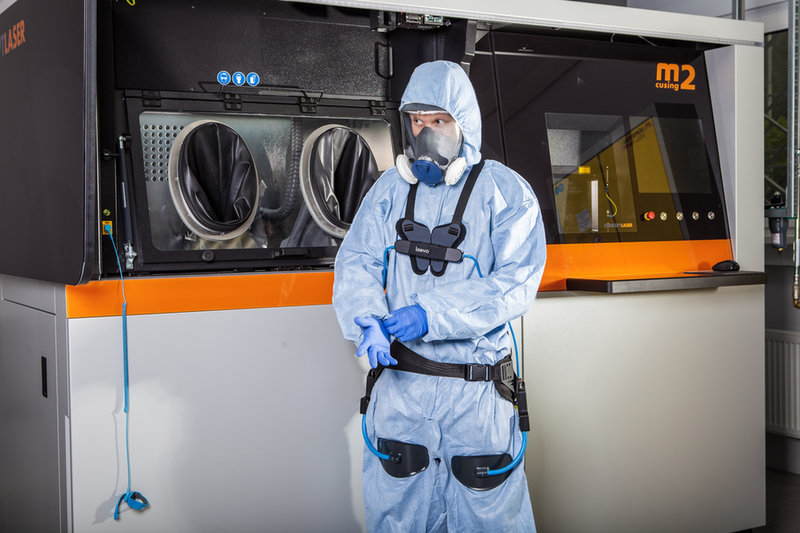
Manufacturing process complies with international quality management standards
Who are the current customers of TEN.MedPrint?
They are the leading post-trauma and reconstruction surgery centers of Russia that use individual additive implants produced by TEN.MedPrint:
- The Blokhin National Medical Research Oncology Center,
- The Russian Ilizarov Scientific Center for Restorative Traumatology and Orthopaedics,
- The Sechenov Clinical Center of the First Moscow State Medical University,
- The Russian Vreden Scientific Research Institute of Traumatology and Orthopaedics,
- Botkin Moscow City Clinical Hospital,
- The Priorov National Medical Research Center for Traumatology and Orthopaedics,
- Turner Scientific Research Institute for Children's Orthopaedics.
What are you betting on? What are the benefits?
We started as a full-cycle company that dealt in engineering and pre-operative models; we would provide the finished product with surgical templates, the navigation system and a relevant specialized tool. However, we eventually decided to focus exclusively on the production of endoprotheses.
Once we stopped handling tasks done by other Russian companies and left only contract manufacturing to ourselves, we saw a dramatic drop in production costs and came off quite efficient in this operation. So now, we are able to offer the best price in the market.
What medical additive products are in demand in Russia?
Individual items:
- oral and maxillofacial surgery
- endoprotheses of major joints such as hip joints
- restoration of large segments of bone after cancer
- cranioplasty
Serial products:
Starting from 2020, intervertebral fusion cages will be serially produced by TEN MedPrint in over 200 types of sizes and in the amount of 4,000 items a year for the Pozvonoq Company.
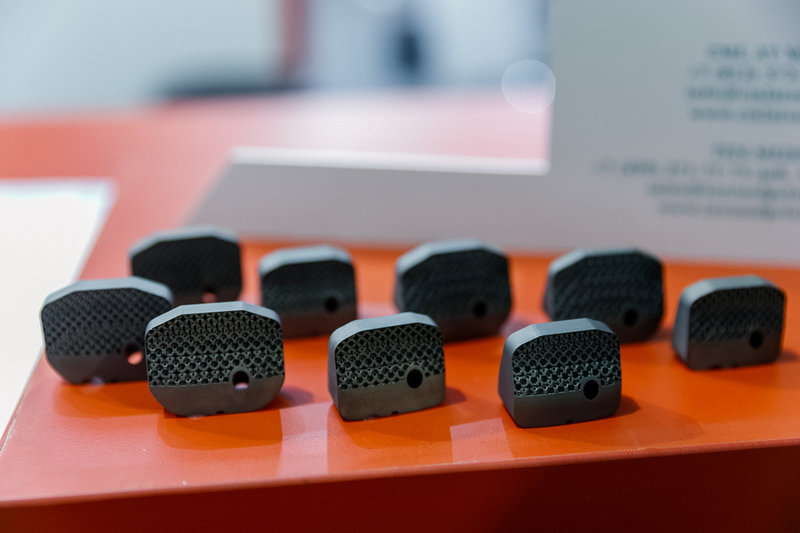
First bench of serially produces additive cages, thousands of items are precontracted
What is TEN.MedPrint all about now?
It is the most efficient team of high tech engineers, two premium-class heavy-duty printers and fully equipped production infrastructure for medical items in compliance with International Standards for quality management control.
Finely tuned cooperation with engineering centers and logistics gives a production time of up to five business days.
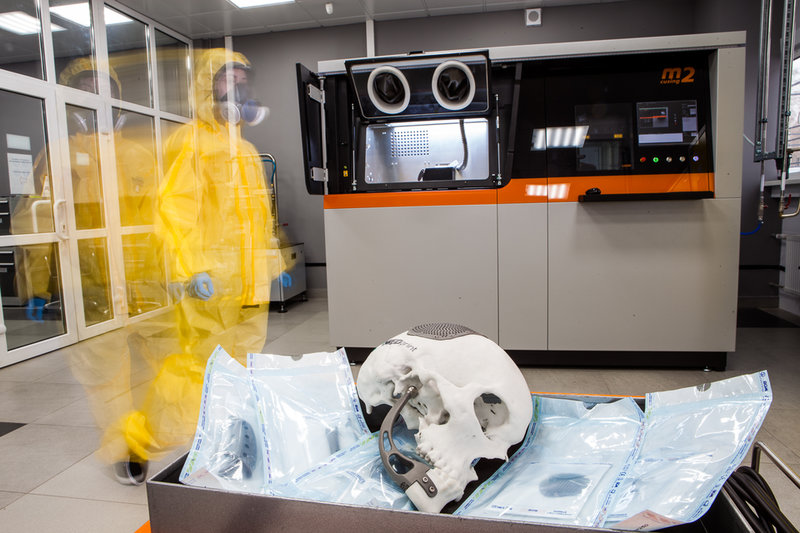
Denis Kovalevich, shareholder:
"It is the fastest growing additive production company of Russia that has obtained all the necessary permissions to manufacture medical endoprotheses, which basically serve as human "spare parts". TEN.MedPrint is at a technological level that allows it to mass-print custom-tailored endoprotheses."
Take a look at the production process at TEN.MedPrint:
- We get a 3D-model from the customer
- We prepare the 3D-model for printing, adding supports and accessories, and calculate the printing time An industrial 3D-printer has a laser that welds titanium-base alloy powder certified for medical use layer after layer
- After the printing process is completed, the platform with the freshly printed items is cleared of the powder. This powder is then cleaned in a special unit to be used again.
- The printed items undergo thermal treatment for better durabilityThey also have to pass the quality control check, which looks into their geometry, density and makes sure there are no misprinted elements
- After the reinforcement stage, the items are stripped of supports and are additionally handled by CNC machines if needed. The implants are then ready for polishing and final cleaning
- The items are sterilized before being shipped to the customer
- They are then packed and sent to the customer together with the relevant accompanying documents (product certificate, ID number, documents for the titanium powder and the conformity certificate)