Compared to screw machines, plastic extrusions tubing and stampings, Braxton's deep-drawing techniques offer many benefits:
- Starting with flat stock and ending with a tubular part, this process minimizes material waste.
- Superior part-to-part and batch-to-batch repeatability are assured.
- Slitting, flaring and hole punching, normally considered secondary operations, can be performed on the drawing machine
- Intricate designs not previously possible can be produced.
- Raw material is work hardened during the drawing process therefore eliminating the need for secondary heat treating on most finished parts.
- Starting stock can be clad or pre-plated with gold prior to the deep-draw process, guaranteeing even coverage of gold on both the OD & lD of micro miniature tubes
- With or without a closed end as small as 0.005" ( 0.13mm) ID . This process also eliminates the threat of residual acid trapped in the parts, a type of contamination that is commonly found in the barrel plating process
Braxton is experienced in drawing a comprehensive range of conventional and special materials including:
- Aluminium
- Beryllium Copper
- Brass
- Bronze
- Copper
- Gilding
- Glass Sealing Alloys 42,52 and Ni/Fe48
- Gold
- Inconel
- Invar
- Kovar
- Monel
- Nichrome
- Nickel
- Nickel Silver
- Phosphor Bronze
- Plated Stock
- Platinum
- Platinum Iridium
- Platinum Rhodium
- Silver
- Stainless Steel
- Titanium
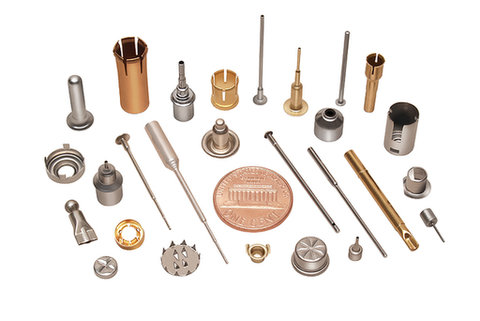
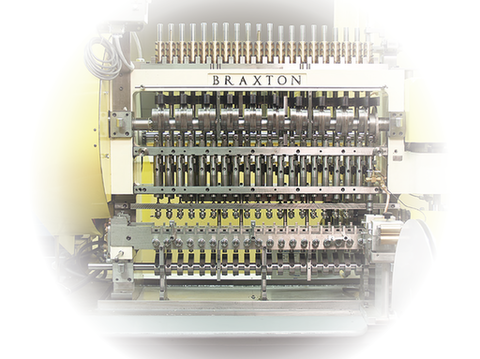
Braxton Manufacturing was founded in 1964 in central Connecticut, an area internationally known as a center of precision tool and die making with a highly skilled work force. In 1972, a second manufacturing facility was opened in southern California to supply deep-drawn components to our growing west coast customer base.
Today, the 60,000-square-foot Watertown, Connecticut facility and the 30,000-square-foot Tustin, California facility are modern, state-of-the-art production plants that provide identical engineering and production capabilities on both coasts. We currently meet the demanding requirements of customers in a wide range of industries, including medical, communications, aerospace, specialty automotive and electronics.
Braxton's engineering department and proprietary drawing machines consistently meet the unique size, tolerance and finish requirements of the most challenging applications. If you have critical parts requirements, contact Braxton today to learn how our precision deep drawing process can provide you with enhanced production efficiencies and cost savings over traditional manufacturing methods.
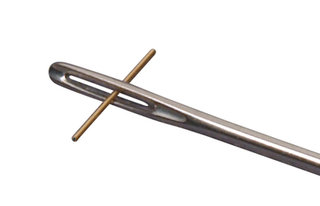
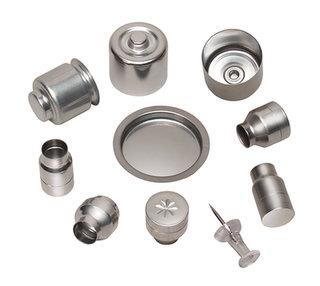
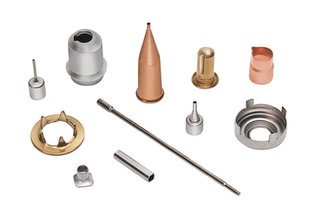
Braxton's Capabilities Maximize the Efficiency of Producing Intricate Components to Meet Your Needs
Critical Dimensions and Tolerances
We can deep-draw parts to 0.006" (0.15mm) OD, with wall thicknesses as low as 0.0005" (0.013mm). Maximum length is 2.250" (57.15mm), and length-to-diameter ratios greater than 55:1 are attainable. Finished part tolerances are as low as ±0.0001" (0.00254mm), with surface finishes to 10 microinches RMS.
Below is a sampling of th
e intricate capabilities that make Braxton the logical choice for your deep-drawn part manufacturing needs, including: working with multiple diameters, knurling, slotting, tabs.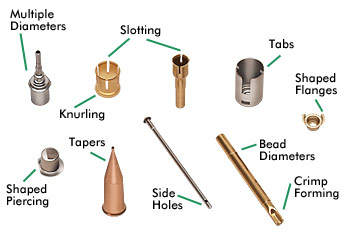
Please visit us at the following trade show exhibitions.
MD&M West, Feb 5-7: Anaheim Convention Center, Anaheim California
IDS, March 12-16: Cologne Germany
Hannover Messe 2019, April 1-5: Hannover Germany
Biomedevice, May 15-16: Boston Convention Center, Boston MA
MD&M East, June 11-13: Jacob Javits Center: New York, NY
EPHJ-EPMT-SMT Salon International Palexpo, June 18-21: Geneva Switzerland
Blech Expo, November 5-8: Stuttgart Germany
Productronica, November 12-15: Munich Germany
Compamed, November 18-21: Dusseldorf Germany
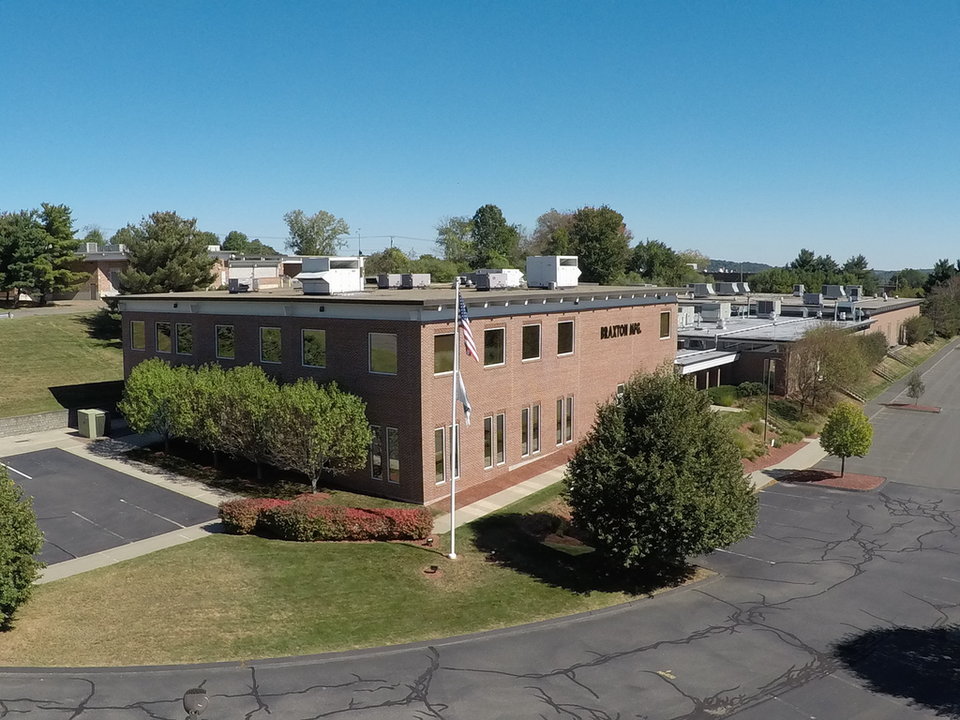
CLICK HERE TO DOWNLOAD THE BROCHURE
CONTACT US