Feature
Next-generation soft robotics for smart healthcare applications
Soft robotics is emerging as a pivotal medical technology due to its biomedical compatibility, ability to adapt to biological environments and enhance safety in human-machine interactions. By Bernard Banga.
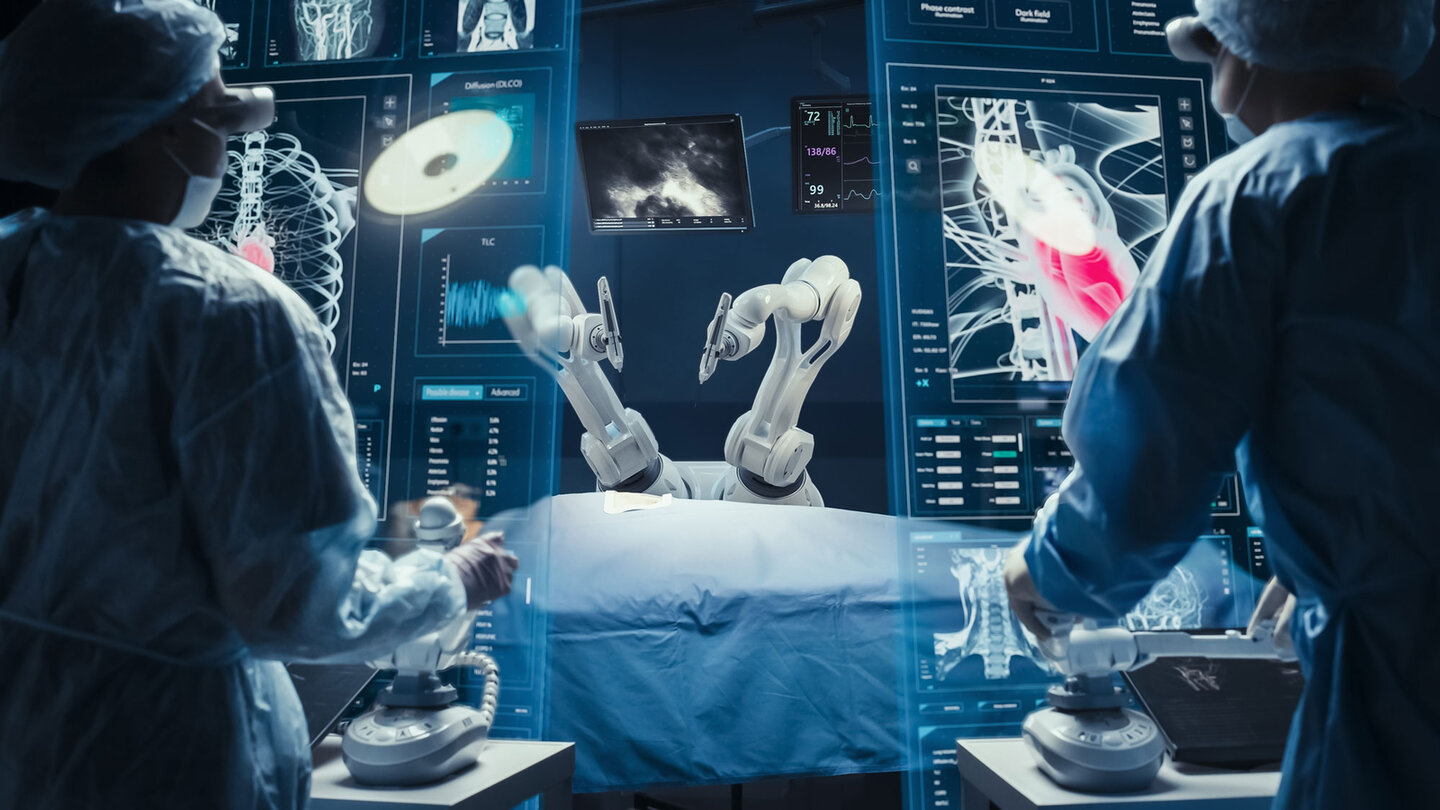
Credit: asharkyu / Shutterstock
Soft robotics is an emerging field that is attracting considerable interest and research due to its inherent flexibility and adaptability. ‘Soft robots offer a higher degree of mechanical variability and plasticity compared to traditional rigid robots and are capable of mimicking the properties of biological tissues and organisms’, explains Zhiyang Lyu, professor at the Jiangsu Key Laboratory for Design and Manufacture of Micro-Nano Biomedical Instruments, School of Mechanical Engineering, Southeast University, Nanjing, China.
Materials and technologies ideal for minimally-invasive surgery applications
‘Soft material and flexible sensors play a key role in enhancing robotic functionality through the integration of soft materials and electronics, improving compliance, adaptability, and human-machine interaction’, explains Jie Yin, associate professor at North Carolina State University, Raleigh, NC, USA. Soft robots rely on novel mechanical metamaterials and elastomers such as silicones and hydrogels, with pneumatic actuation being a dominant method in this field.
Shape-memory alloys (SMAs) and shape-memory polymers (SMPs) offer advantages such as high power density and diverse actuation motions, making them alternatives to traditional actuators due to their scalability, lightweight components and stability in various environments. Recent developments in SMA technology, such as nitinol wire-based torsion springs for image-guided surgery, highlight the miniaturisation potential of these materials, with 200 μm Cu-based crystals enabling precise microscale applications.
Soft robots are ideal for minimally invasive surgical tools and can use a range of actuation methods, including hydraulic systems with fluid elastics, electric actuation using electroactive polymers, and more recently, magnetic actuation. Piezoelectric materials such as lead zirconium titanate (PZT) and polyvinylidene difluoride (PVDF) remain common, while ionic polymer–metal composites (IPMCs) are emerging due to their excellent electromechanical properties, which Lyu explains make them promising candidates for soft robotic actuation.
Advances in soft robotics through 3D printing and biocompatible microdevices
‘A main challenge in the development of biocompatible micromachines arises from engineering biological materials at the micro and nanoscale and integrating those materials into devices’, explains Holly M. Golecki, teaching assistant professor at the University of Illinois Urbana-Champaign. Recent advances in 3D printing offer a promising platform for manufacturing miniature soft robots by leveraging the printability of materials such as nanomaterials, stimuli-responsive substances and biomaterials. These technologies enable high-resolution, accurate printing.
Techniques for 3D bioprinting at the micrometre scale have advanced, successfully producing complex biological structures such as vascular networks and organ scaffolds. One key manufacturing technique, the 3D PICL μM (3D printing, ink casting and micromachined lamination) process, is used to create devices such as microelectrode arrays, microneedles and microfluidic chips. These microdevices offer numerous potential applications, notably in electrophysiology, organ simulation, drug delivery and gene testing. Hybrid 3D printing is also being used to prototype microfluidic systems, including finger-actuated pumps, fluidic couplers and nucleic acid amplification test devices, further pushing the boundaries of micromachine applications in medicine.
Nanofibres and colloidal self-assembly: pioneering biohybrid implants and soft micro-robotics
Electrospinning enables the precise fabrication of nanofibres for soft robotic components at both the micro- and nano-scale, offering meticulous control over the diameter, shape, structure and alignment of the fibres. This degree of precision supports the miniaturisation of pneumatic actuators, paving the way for the development of micrometre-scale soft robotic grippers. Colloidal particle self-assembly, whether active or passive, and responsive to external stimuli such as light, also mimics natural processes to generate intricate structures with the ability to perform collective functions.
‘This assembly is controlled by instigating light-responsive interactions in the swarm and can be controlled remotely with high precision using optical forces, photochemical reactions, photothermal effects, and photoisomerization’, explains Golecki. This technique can be used to produce adaptive materials and reconfigurable robots that can be used for tasks such as micro- and nano-scale manipulation and transport.
‘Soft microrobotic artificial muscles, as well as other soft microrobotic devices can be developed using the colloidal nanoparticles as “building blocks”’, Golecki continues, highlighting their transformative potential in advanced applications. The field is progressing towards biohybrid implants and soft biohybrid robots, which integrate both biological and synthetic components, spanning the molecular to cellular and tissue scales. ‘[These biohybrid systems] will be integrated with patients to provide longitudinal health monitoring and modulation’, predicts Dr Ritu Raman of the Massachusetts Institute of Technology (MIT) Department of Mechanical Engineering, Cambridge, MA, USA.
From exoskeletons to biomimetic organs: soft robotics in modern rehabilitation
Soft robotics have made substantial contributions to patient rehabilitation, particularly in enhancing physical therapy. ‘Soft arms help in physical therapy by accompanying and guiding rehabilitation movements of distal limbs’, explains Dr Ritu Raman of the Massachusetts Institute of Technology (MIT) Department of Mechanical Engineering, Cambridge, MA, USA. Wearable soft exoskeletons further empower individuals with mobility impairments, enabling them to perform daily tasks more easily. Soft robotic technologies have also been used to create biomimetic organs, such as heart models and laryngeal simulators, which serve ‘as models to study pathologies or as prostheses to restore physiologic function’, Raman concludes.
AI and machine learning in soft robotics: overcoming complex challenges
Similar to living organisms with inherent biological self-sensing, neural processing and autonomous decision-making capabilities, miniature soft robots can achieve independent behaviours using artificial intelligence (AI).
Over the past decade, machine learning has been extensively studied and applied to the design of soft robots. ‘Favored by machine learning with prestored or ongoing corrected datasets, soft robots can be facilitated to achieve high-level planning, control, state estimation capabilities, and address hysteresis and nonstationary issues’, explains Jie Yin, associate professor in the Department of Mechanical and Aerospace Engineering at North Carolina State University, Raleigh, NC, USA.
There are three primary approaches to integrating intelligent control into robotic systems: learning the inverse kinematics or statics of the end effectors, learning forward dynamics to predict control outcomes, or direct learning from human controllers. According to a 2020 paper by researchers from the Department of Mechanical Engineering at Carnegie Mellon University, Pittsburgh, PA, USA, the application of data-driven machine learning techniques has significantly improved traditional soft robots, enabling precise manipulation and reducing the risk of dynamic failure.
‘Given the generality, machine learning techniques are expected to benefit the future designs of miniature soft robots with more intelligent control systems for complex tasks’, concludes Yin.
“We do this all virtually on the computer, so we can make the osteotomy in multiple different places to decide where the most appropriate place to do the correction is.”
From here, relevant standard orthopaedic plates are selected for use in the surgery.
Following these preliminaries, surgical guides, jigs, and plastic models of the patient’s anatomy, in this first case the radius, are 3D printed and then sterilised for use in surgery.
“We make sure that the guide fits the bone in the patient exactly the way we planned for it to fit on the plastic bone. Once we have made sure that’s the case, we secure the guide to the bone with wires, and then we do whatever the plan has been,” says Lattanza.
In osteotomy, such plans generally involve drilling holes and then making the necessary bone cuts.
The great thing about this approach, Lattanza states, is that all that needs to be done to ensure the correction has been completed as planned during the surgery is to line up those holes.
She explains: “If the bone is rotated off 90° and when we drill those holes, they’re off 90° on the bone, we make the cut then we rotate and line up those holes to put the plate on because the plate holes are straight, and that’s how we know that we’ve got the correction.”
Beyond making relatively common osteotomies more accurate, a 3D provision also allows for more complex cases to be worked upon. Lattanza relays a recent case in which a child had broken the radius and ulna bones in their forearm.
“During the time that she was growing, this deformity got ‘very 3D’, meaning it was off in the sagittal, coronal, and axial plane,” says Lattanza.
“You can’t see the axial plane on an X-ray, and if you can’t see it, you can’t correct it.”
In this case, the procedure required two cuts in the radius to restore it to normal anatomy, and one in the ulna.
“In my career prior to having the 3D technology, that’s something that is difficult or impossible to plan and to execute in the operating room, because you wouldn’t even be able to see that you needed two cuts to make it normal again,” explains Lattanza.
Lattanza is keen to add that the influence of 3D printing on preoperative planning and during surgery should not be a cause for complacency, particularly given that there remain limitations to 3D visualisations of CT scans, chiefly in that the current technology cannot show soft tissue.
“Some people think that this is kind of a phone it in now, but that’s not how it works,” she says.
“This is a collaboration between an engineer and a surgeon, and it has to be that way to get a good result.”
Once we see where those changes are, we can plan where we’re going to cut the bone.
Dr Lattanza
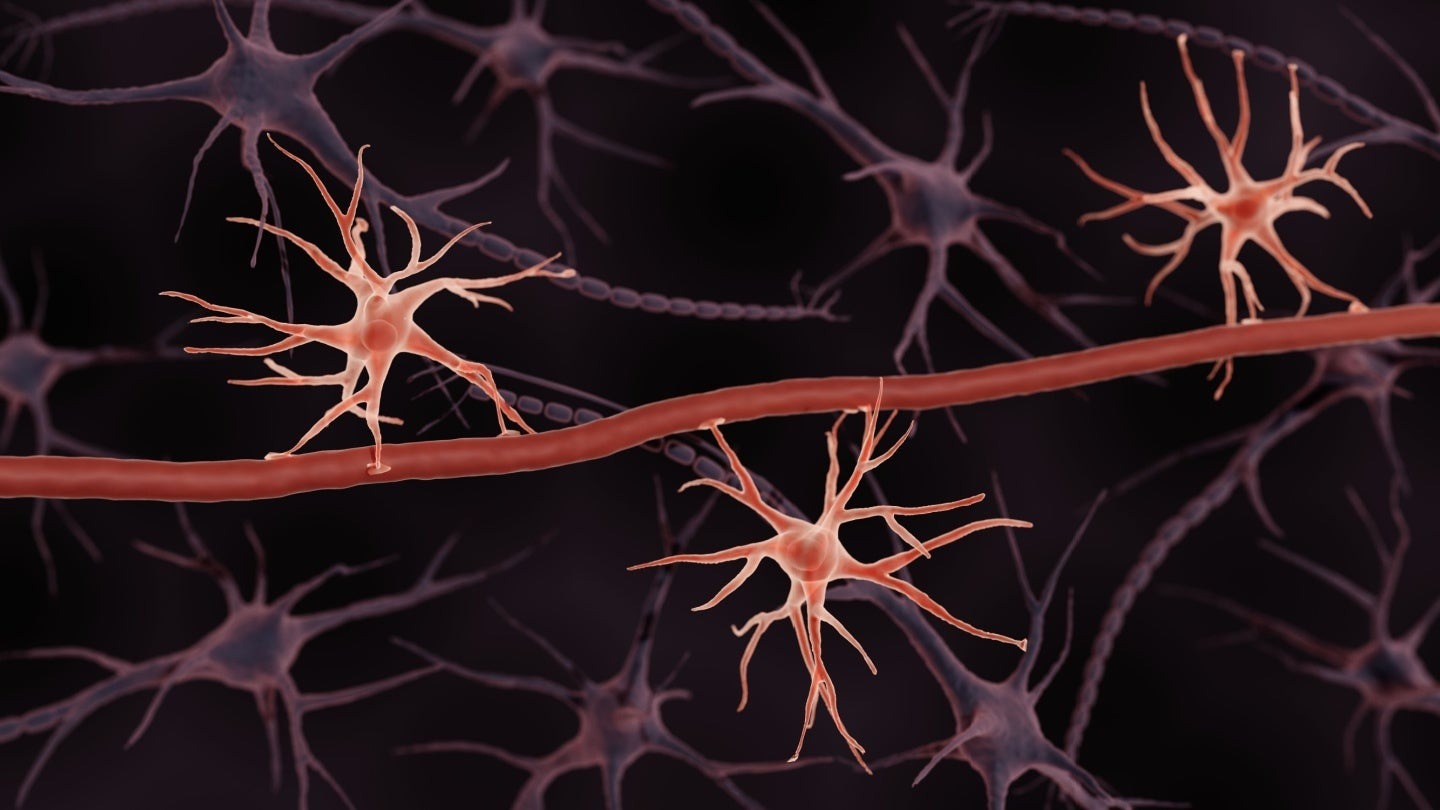
Astrocytes are a type of neural cell that builds the BBB, and Excellio plans to derive exosomes from them to make them even better at targeting the brain. Credit: ART-ur / Shutterstock
Caption. Credit:
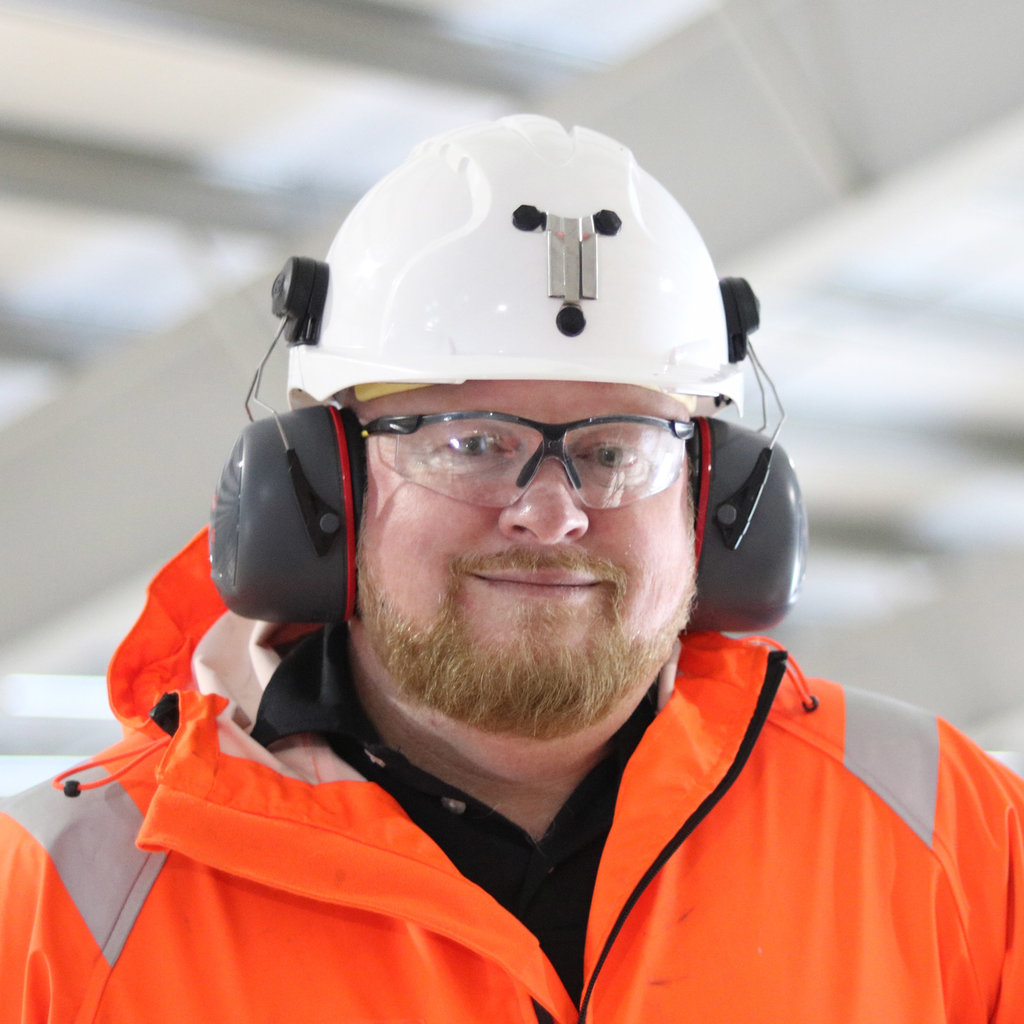
Phillip Day. Credit: Scotgold Resources
Total annual production
Australia could be one of the main beneficiaries of this dramatic increase in demand, where private companies and local governments alike are eager to expand the country’s nascent rare earths production. In 2021, Australia produced the fourth-most rare earths in the world. It’s total annual production of 19,958 tonnes remains significantly less than the mammoth 152,407 tonnes produced by China, but a dramatic improvement over the 1,995 tonnes produced domestically in 2011.
The dominance of China in the rare earths space has also encouraged other countries, notably the US, to look further afield for rare earth deposits to diversify their supply of the increasingly vital minerals. With the US eager to ringfence rare earth production within its allies as part of the Inflation Reduction Act, including potentially allowing the Department of Defense to invest in Australian rare earths, there could be an unexpected windfall for Australian rare earths producers.